Lubricants and fuels
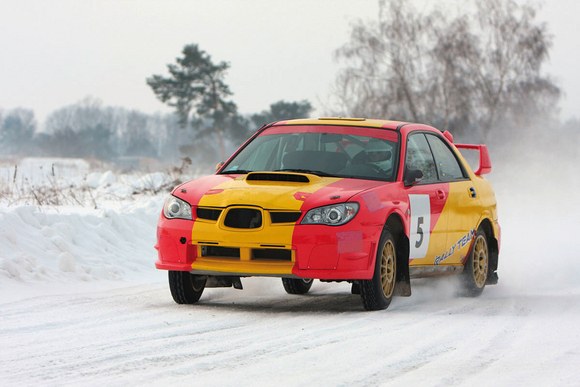
Viscosity index and kinematic viscosities of SAE/ISO motor oils at application temperatures
The Viscosity Index VI is used as a measure for the temperature dependence of the viscosity with lubricating oils in the area of application. In accordance with ASTM D 2270 or ISO 2909, this is determined from the kinematic viscosities at 40 and 100 °C. Here, oil with the least change in viscosity was assigned a VI value of 100, while that with the largest change was assigned a VI value of 0. With modern synthetic oils or multi-purpose oils the viscosity index can be increased significantly above 100 using additives (VI improvers). The higher the viscosity index of an oil, the less its viscosity changes at different temperatures. This makes the operation of engines, for example, less subject to climatic conditions. In summer, the lubrication effect of such oils is still sufficient, while in winter the oils are not too viscous.
Depending on the sample rate, the LAUDA PVS system provides tailored solutions. As such, a PVS system in a PV 15 viscothermostat can be used to program the necessary temperatures of 40 and 100 °C while measuring the viscosities of the same samples one after the other. The two values, and thus the viscosity index, can be determined significantly quicker when measuring stands in two thermostats are used at fixed temperatures of 40 and 100 °C. This way, oils can be measured using a PVS 1/8, each with four measuring stations at 40 and 100 °C in two thermostats along the entire viscosity range. If equipped accordingly, the glass capillary viscometers are then cleaned and dried automatically.
Recommended standards
- ISO 2909
Petroleum products – Calculation of viscosity index from kinematic viscosity
- ASTM D 2270
Standard Practice for Calculating Viscosity Index From Kinematic Viscosity at 40 and 100 °C
Typical configuration
Measuring system PVS 1/8 with four + four measuring stands for parallel measuring of viscosities at 40 and 100 °C and calculation of the VI index with automatic viscometer cleaning for oils from 2 to 1,000 mm2/s
- PVS 1/8 control unit
- Eight measuring stands S 5
- Software module VID-DLL
- Four VRM 4 cleaning modules for cleaning the Ubbelohde with two cleaning agents
- Two PV 24 viscothermostats (one at 40 °C with water and DLK 10 cooler and one at 100 °C with thermostating oil)
- Two Ubbelohde glass viscometers each of sizes Ic, II, IIc, III (with aspirating tube)
- Dosing syringes for filling the viscometers
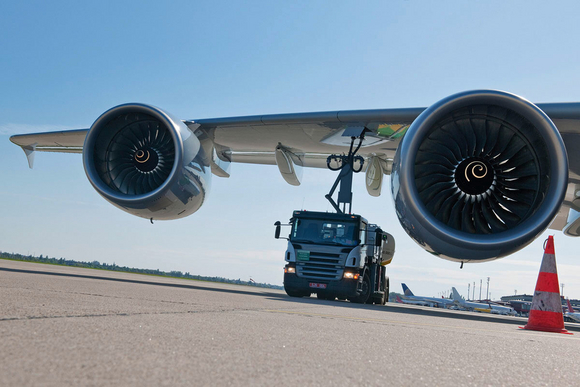
Low-temperature behavior (paraffin formation) of motor oils, diesel, and kerosene
In modern aviation, extreme requirements are made of both the technology and the materials. At the flying altitudes of today‘s jets at 10,000 meters, temperatures down to -60 °C are common. Luckily, it is not the passengers who feel the effects of this, but the fuel in the tanks and piping as well as the motor and drive lubricants. As such, it needs to be ensured that their viscosity does not increase to a level over a critical value or that the paraffin begins flocculating as a result of the extreme temperature changes during long flights. For this reason, tests on the viscosity are carried out in the lab in realistic conditions. Of course, the same applies to fuels, and motor and hydraulic oils which are used in polar regions, meaning that viscosity measuring down to -40 °C is also relevant here.
In connection with the powerful DLK 45 through-flow cooler or the Proline RP 890 cooling thermostat, the PVL 15 viscothermostats for two measuring stations and PVL 24 for four measuring stands are designed for working at temperatures down to -40 or -60 °C. The four-fold insulating glass prevents the windows from fogging up and makes sure the viscometers can be seen clearly. With the PVS system, kinematic viscosities at these extreme temperatures can be measured conveniently. The viscometer is cleaned automatically too. The ambient air used in measuring and cleaning can be dried using a connected cooling trap so as to avoid any freezing, especially of the measuring capillaries.
Recommended standards
- ASTM D 2532
Standard Test Method for Viscosity and Viscosity Change After Standing at Low Temperature of Aircraft Turbine Lubricants
- ASTM D 445
Standard Test Method for Kinematic Viscosity of Transparent and Opaque Liquids (and Calculation of Dynamic Viscosity)
Typical configuration
Measuring system PVS 1/2 with two measuring stands for parallel measurement of viscosities at temperatures down to -40 °C with automatic viscometer cleaning and drying trap for kerosene and other fuels.
- PVS 1/2 control unit
- Two measuring stands S 5
- A VRM 4 cleaning module for cleaning the Ubbelohde with two cleaning agents
- PVL 15 viscothermostat connected to a powerful cooler
- Two Ubbelohde glass viscometers each of sizes Ic, II (with aspirating tube)
- Cooling trap for drying and cleaning the used ambient air
Applications Lubricants, oils and fuels
Pumpability of crude oils (record of viscosity temperature characteristics)
Absolute, kinematic, and dynamic viscosities of highly viscous liquids